Shell and Tube Heat Exchangers: Design, Function, and Applications
The Shell and Tube Heat Exchanger plays an important role in various industries, like chemical processing to HVAC systems. These versatile systems are designed to efficiently transfer heat between fluids without mixing them, making them indispensable in various applications. In this blog, we’ll dive into how Shell and Tube Heat Exchangers are work, their key components, and how to choose the right one as per your needs.
How Shell and Tube Heat Exchangers Work
It is a strong design used to transfer heat between two fluids, and it works so precisely that it does not mix with the other. The process begins when one fluid enters the system through the header, flowing through the tubes. Simultaneously, the second fluid will enter the shell and surround the tube from outside. Core components are held by tube bundles, whereas the shell surrounds the exchanger. It has two ends, front and back, for the fluid's entry and exit. It easily handles high and low pressure. Its header as well as the tube can be removed for cleaning, repairing and maintaining.
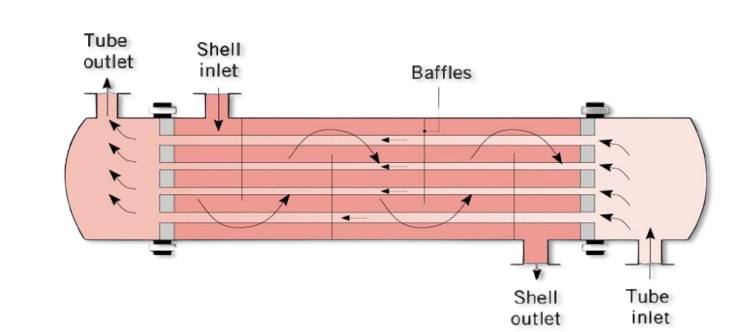
Why are Shell and Tube Heat Exchangers Widely Used?
Its modular design helps it to update to different designs as per the needs of the business. This flexibility helps it to handle different types of fluids and gases by adjusting its internal tube and external shells. It is used to maximize heat transfer between two fluids. It transfers heat efficiently from hot to cold fluids, which leads to effective heating and cooling. It has a compact design, but it is customized as per the requirements of space. Even under extreme environments, no chemical corrosion or high temperature fluid can affect the exchanger. It can be easily dismantled for cleaning and maintaining. It is designed to save energy and increase the production level. Because of its build quality, it serves a long period of time.
Key Components of Shell and Tube Heat Exchanger
The main constituents of a shell and tube heat exchanger include:
- Tubes: These are fundamental heat change units, straight or U-shaped, bent into triangular, square, or turned-square shapes to conduct heat. Finned tubes find wide application in hot conditions to deliver maximum heat exchange efficiency.
- Shell: The big cylindrical outer casing contains the tube bundle. It directs the shell-side fluid flow and is used mainly in tough materials like carbon steel or special alloys for toughness and durability.
- Baffles: Internal plates that direct the shell-side fluid through the exchanger. They cause fluid turbulence, enhance heat transfer, and help to support the tubes against vibration and sag.
- Single Segmental
- Double Segmental
- Disc and Doughnut.
- Orifice Baffle
- Rod Baffle
- Tube Sheets: Heavy metal plates on both sides of the exchanger housing the tubes. They are designed to keep the tube side and shell side fluids away from one another to prevent mixing.
- Channel Partition Plates: Employed in multi-pass use, these plates split the tube-side fluid flow into more than one pass or section. It maximizes the fluid time to optimize the heat transfer technology in the exchanger.

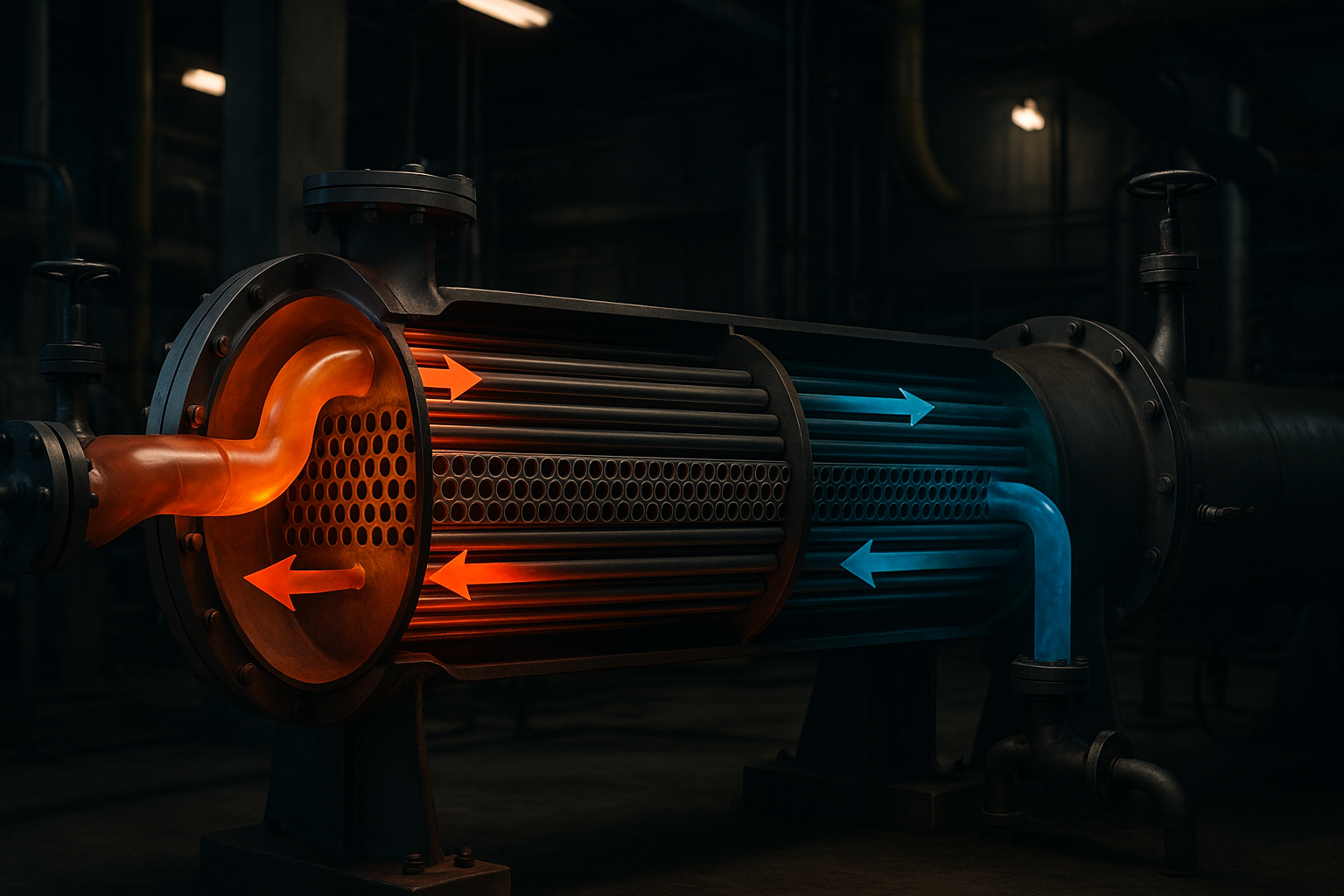
Types of Shell and Tube Heat Exchanger:
Sr.No. | Type | Material | Usage/Application | Medium Used |
---|---|---|---|---|
1 | Fixed Tube Sheet | Carbon Steel, Stainless Steel | Chemical Processing, Oil Refineries, HVAC | Water, Oil, Steam, Chemicals |
2 | Floating Head | Stainless Steel, Hastelloy, Inconel | High-Temperature Applications, Power Generation | Steam, Hot Gases, Corrosive fluids |
3 | U-Tube | Stainless Steel, Copper Alloys | Pharmaceutical, Food Processing, HVAC | Water, Food-Grade Liquids, Refrigerants |
4 | Kettle Type | Stainless Steel, Zirconium | Petrochemical, Evaporators, Reboilers | Steam, Chemicals, Hydrocarbons |
How to Choose the Right Heat Exchanger for Your Needs
This thing you must consider while designing a shell and tube heat exchanger to suit your needs.
- Recognize what your process fluids and operating conditions are. This will determine the correct design and construction materials for your heat exchanger.
- Always make sure that the materials selected is appropriate and of good quality. This will be according to your application, i.e., the requirement for corrosion-resistant alloys in harsh environments.
- Consider your future needs and potential expansion plans. You want your heat exchanger to handle changes in your process.
- Understand your budget. Equate your needs and cost, and lead time so that you obtain the product that you require. Work with reliable manufacturers and suppliers. Always buy from trusted sellers.
Trends in Shell and Tube Heat Exchanger: Innovations and Advancements
- IoT Integration and Digital Monitoring: Facilitates real-time performance monitoring, predictive maintenance, and optimization.
- Monitor performance
- Predict maintenance needs
- Optimize heat transfer
- Sustainability Focus: Focus on energy-efficient designs, green materials (such as stainless steel), and heat recovery systems.
- Energy-saving designs
- Use of environmentally friendly materials
- Heat recovery systems
- Customization: Increasing demand for heat exchangers that are customized to individual fluids, temperatures, and pressures for special industrial applications.
- Modular designs
- Customization based on process needs
- Advanced Materials: Application of corrosion-resistant alloys and specialized coatings to enhance durability and resist harsh environments.
- Alloy development
- Coatings for corrosion resistance
- Innovative tube materials
- Compact Designs: Space-saving, high-performance heat exchangers with higher heat transfer surfaces.
- Smaller footprints
- Enhanced heat transfer surfaces
- Automation Integration: Heat exchangers are becoming part of more extensive process control systems for maximizing performance efficiency.
- Better process optimization
- Seamless monitoring and control
- Safety and Compliance: More emphasis on complying with international standards (e.g., TEMA, ASME) for improved safety and regulatory compliance.
- Compliance with industry standards
- Enhanced safety features
Why Choose Us?
Upase Process Equipments is one of the top leading shell and tube heat exchanger manufacturers in Pune & suppliers in Pune, India. We provide you with a quality product that is also durable and provide custom-built designs as per the client's requirements. We keep the opinions of our clients and use them to build a quality machine. Quality materials such as carbon steel and stainless steel are used to build industrial heat exchangers. We upgrade ourselves with the future trends and features in the market.
Shell and Tube Heat Exchangers are vital to many industrial applications due to their flexibility, durability, and efficient heat transfer capabilities. Whether you're looking to optimize your existing systems or need a custom solution for specific requirements, it’s essential to choose a high-quality heat exchanger design for your unique process. Get in touch with us now to discover more about how we can assist you in finding the ideal industrial heat exchanger to suit your requirements.